Maintaining your equipment is an unsung but essential part of running a dental practice. Simply put, if your equipment isn’t working, you can’t work on patients. The expense of replacing equipment can run into the hundreds and thousands of dollars, making it sound financial management to prioritize equipment maintenance. The cost of losing a customer because your equipment wasn’t working when you needed it can be even higher than the cost of replacing equipment. Fortunately, it’s easy to maintain your equipment if you follow a few best practices. Following a maintenance schedule, keeping a maintenance kit on hand and using automated tools to implement your schedule will help ensure that you keep your equipment in top working condition.
Table of Contents
Create a Maintenance Schedule Checklist
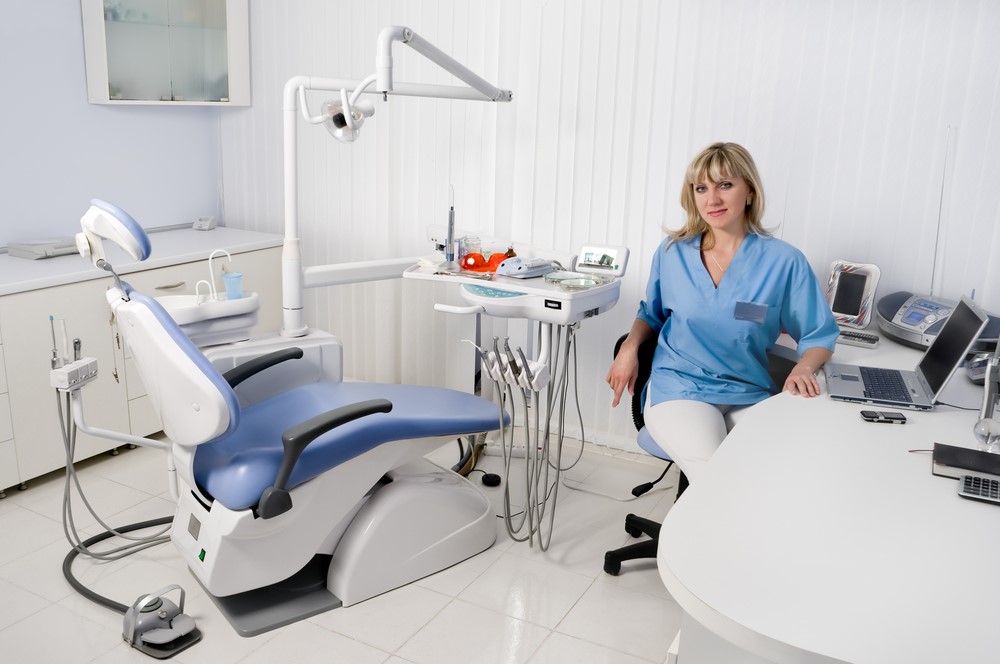
With hundreds of different pieces of equipment in your dental clinic, the only way to make sure everything gets taken care of is to use a maintenance checklist. Your checklist should cover everything that needs periodic review, repair or replacement. The most efficient way to organize your checklist is to group it into items that need daily, weekly, monthly and annual attention. Daily items can include:
- Flushing water through syringes
- Flushing water through handpieces, sterilizing them and lubricating them
- Flushing handpiece waterlines after each patient uses them
- Lubricating prophy and contra angles and nose cones after use
- Disinfecting operatory equipment after use
- Using suction cleaner on high volume evacuators and saliva ejector tubings
- Cleaning traps on delivery units
- Draining and cleaning ultrasonic cleaners
- Checking and disposing of containers for hazardous waste, infectious waste and needles and other sharp objects
Weekly items can include:
- Checking handpiece gaskets and replacing any that need it
- Checking o-rings on handpiece couplers and replacing any that need it
- Testing sterilizers for biological spores
- Changing delivery unit traps
- Inspecting for safety hazards in the workplace, such as obstructed paths, spills or loose rugs
Monthly items can include:
- Sitting in patient’s chair to review how the office looks and see what needs cleaning
- Cleaning plaster traps and master traps
- Cleaning model trimmers
- Cleaning radiology cassettes and intensifying screens
- Checking working condition of patient monitoring equipment
- Checking working condition of anesthesiology equipment
Annual items can include:
- Changing cassette seals and gaskets for sterilizer doors
- Changing compressor oil
- Inspecting x-ray equipment
- Inspecting emergency fire, smoke and lighting systems
- Reviewing compliance with state, OSHA and HIPAA regulations
- Sending your employees to the OSHA 10 hour and OSHA 30 training courses to ensure they have a full understanding of the best safety practices available.
Use this list as a starting point, and include any other items that apply to your office. You can write your checklist by hand, but for best results, use an electronic format such as a spreadsheet or app.
Keep a Maintenance Kit on Hand
In addition to routine maintenance tasks, there are occasional repair needs that may arise unexpectedly, and can set your schedule back if you don’t have a prompt solution. To prepare for this, you should keep a maintenance kit on hand. Your kit should include items such as:
- Extra o-rings and gaskets
- Handpiece cleaners, lubes and replacement turbines and chucks along with bur tools for replacing them
- Extra light bulbs for handpieces, operatory lights and curing lights
- Vacuum line cleaners, air filters, canisters and traps
- Air compressor intake valves and oil
Having these items on hand will help you avoid unpleasant emergencies that can throw off your whole patient schedule and potentially cost you customers.
Automate Your Maintenance Scheduling
Because there are so many maintenance items to remember and schedule, it’s advisable to have a system in place to make sure tasks get done on time. Automation can assist you in making this chore easier.
One of the simplest ways to use automation for maintenance scheduling is to create a maintenance log in an Excel spreadsheet. List your maintenance tasks in rows, with column headings indicating whether the task should be done daily, weekly, monthly or annually. When a task is completed, mark the date in the corresponding cell. Be sure to keep copies of your logs for future reference.
Another way to use automation to help you implement your maintenance schedule is to use a reminder app that sends you automatic notifications when a task is scheduled. A more sophisticated version of this strategy is to use specialized equipment maintenance software, which can include features such as work order management and warranty tracking in addition to automated reminders.
A comprehensive checklist forms the foundation for scheduling routine maintenance tasks. Keeping a maintenance kit on hand ensures that you have the tools you need to clean, repair and replace your equipment when you need to. Using automated tools for notifications and tracking will help make sure that essential maintenance tasks get done on time, keeping your equipment ready when you need it and extending its lifespan to save you money on replacement costs.